“减少”当然是一个流行词高效电动机的设计师之一。他们想降低成本,当然,也减少核心损失和装配尺寸。
那么,“可能吗?”
的一个常见的抱怨轴电机工程师使用传统钢薄板选项的笨重的本质工作堆积大量的限制为单个组件完成。这是一个三方共享头痛薄板装配选项在下面的图表中我们比较。然而,我们也会比较non-lamination替代—软磁复合材料出名的材料,减少组件的数量在一个交流定子或转子设计。
让我们回顾一个视觉并排的电动马达组装过程:
电机装配过程图,轴向磁通电机设计
这是我们处理步骤,优点,缺点:
- 成卷带钢组装
- 标准钢板装配
- 钢板用垂直层压杆组装
- 粉末金属软磁复合材料
上面完成的图像可能是你梦想的一部分将如何走到一起。然而,有一种误解的成本和易于制造一个电动马达。
选项一:Mandrel-Wrap长条状的薄钢板
这个过程,典型的轴向磁通电机设计,包括包装芯棒周围的磁性材料,焊接,加工出杆件。退火之后可能是必要的,以减少核心损失和提高磁性性能。
虽然过程不是太困难的从开始到结束,它缺乏波兰。最优先考虑的问题是:
- 材料效率低下——高达50%的废品废料
- 做空包裹层之间
- 高核心损失,降低电动机的效率

选项B:径向叠加纹理钢
这个过程开始于平坦,叠层电炉钢表。制造商邮票出必要的形状、种类,组装在径向方向。再次,退火可能需要保持磁性性能。
该方法使用钢薄板是友善的钱包从材料使用的角度来看。不幸的是,它的效率在其他方面:
- 排序和组装很麻烦
- 铆合上胶、焊接和子组件可以减少磁性性能
- 最不理想的磁通方向
本届大会在径向磁通电机设计方法很常见,当然足够当高性能是没有必要的。如果你需要更多效率更高的频率,继续向右移动图表。
选择C:垂直堆叠纹理钢
现在我们已经取得了一些进展。
这个电机装配过程是像过去一样,除了它使用垂直层压杆。
和之前一样,制造商邮票的不同大小的薄片,然后通过焊接组装他们或另一个加入的过程。有一个额外的步骤加工内外直径,并可能退火。
像上面的径向叠选项中,该垂直选项更有效地使用材料相比,盘绕组装。与径向叠加,垂直叠加允许适当的取向的波兰人磁通量携带,同时保持运营效率。
它还达不到理想的解决方案吗?
- 高成本组装
- 潜在的劳动密集型
- 核心的损失还是一个问题
选择D:软磁复合粉末
最后,我们来到软磁复合材料(smc)。这个家庭电动马达的核心材料包括粉末粒子一个电绝缘涂膜处理。
与层压、粉末金属(smc)创建部分通过一个添加剂的过程,而不是减法。粉末冶金制造小型汽车只需要材料形成最后一部分,然后热对待和处理任何必要的装配。
先进的粉末冶金帮助smc的许多优点胜过薄片在交流电动机设计:
- 优化磁通路径——叠层板定位不是一个因素,所以通量流无论你想要的
- 更可靠的核心损失减少——空气间隙中形成复合大大减少渗透策略上额外的床单
- 有用的频率达到和超过2000赫兹
- 95% +材料效率
- 近净成形能力对于复杂的、独特的几何图形
- 长部分不降低性能
最后一点可能会引起过多的关注。一些工程师认为粉末冶金为他们的项目不是一个选择,因为part-size局限性。实际上,通过市场细分,SMC部分绕组可以方便容易核心,减少进一步的损失。
因为很少在制造一个完美的解决方案,我们应该知道smc有一个缺点:降低强度。smc不能烧结,提高强度,高温会使最终的组件过度损耗。
考虑您的应用程序的最终用途,是否上面的很多好处大于适度降低强度。
今天(明天&)电机材料的作用
的效率“电气化”继续发展,电动马达材料可以,魔术的关键字“减少”。
减少装配步骤,减少固有的核心的损失和资源的浪费,纹理的过程,与今天的粉末冶金是可以实现的。交流电动机装配与smc,“可能的”很容易。
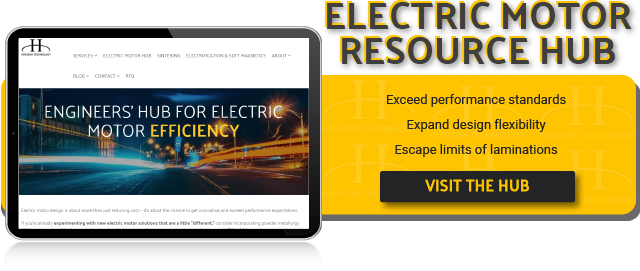